Put the pedal to the metal, they say…we help put rubber on the pedal.
INTRODUCTION
Manufacturing automotive parts, i.e., pedals, clutches, accelerators, and brakes, can reveal a tough challenge, for they are all components that need to endure countless applications at each and every use. Therefore, they have to withstand the test of time and be highly wear-resistant, as poor performance can jeopardize the safety of the user. As a consequence, their design and production materials are quintessential. Vehicle pedals, for example, can be produced with different materials, such as steel, or composite materials – as is the case with modern cars, where manufacturers strive to find a balance between reducing weight and minimizing costs. In certain specific fields of application – e.g., farm vehicles – they take advantage of rubber covers to improve performance. The rubber compound in use and their specific features have, therefore, to be designed and planned accordingly, in order to meet the application needs. Which is where molds come into play.
Why do pedals have to be covered with rubber in the first place?
Rubber-compounds covers for pedals, especially those found in agricultural tractors, are a necessary component to ensure user comfort and safety, as well as maximize efficiency, as these types of vehicles usually undergo extreme stresses not commonly experienced in your average utility vehicle or sedan.
PEDALS: AN UNDERRATED DEVICE?
To choose the best compound for your tractor pedals, it is first necessary to have a thorough understanding of the mechanics of the pedal in question, their purpose, use, structural and mechanical features, for it is important to find the right balance between comfort, efficiency, resistance and durability, precision and control, and costs. There’s a lot going on when dealing with the production of a pedal, so let’s explore some key aspects involved in more detail.
-
Ergonomics and Comfort:
- Pedal Shape and Size: First thing first, tractor pedals should always be designed with ergonomics in mind. As a matter of fact, their shape and size can impact the operator’s comfort. Dimensional features are a key element to take into consideration to balance efficiency and costs.
- Cushioning Materials: The rubber covering the pedal should provide adequate cushioning to reduce discomfort during prolonged use. When budgeting a supply for your rubber covers, you may want to consider aspects such as pedal dimensions beforehand, and then cover thickness. Finding the right thickness is crucial, for it can vary depending on many other factors, including density, viscosity, as well as other chemical features, which can impact on purchasing costs of both the compound, mold making, and molding. Different compounds may, in fact, entail differences in the production processes of both the final item and the mold itself.
- Adjustability: Some pedals have adjustable height or angle to accommodate different operators’ preferences. How does this impact operability? Does the rubber cover need to have more grip? This may entail a) choosing a rubber compound with higher adhesion, b) changing the cover design and geometry, e.g., adding a knurled surface. To produce knurled surfaces, the mold may need to undergo EDM electrochemical treatment , which has an effect on costs.
EDM machine at our production facility. In the middle, you can see a steel mold loaded and ready to be plunged into the electroerosion liquid.
-
Safety Features:
- Anti-Slip Surface: anti-slip texture is, in any case, a must-have feature on pedals for agricultural machinery, as this is an fundamental safety feature to prevent the operator’s foot from slipping, especially in wet or muddy conditions.
- Visibility: The pedal should be clearly visible to the operator even in low-light conditions.
- Pedal Extensions: In some cases, removable pedal extensions can be added to improve reachability for operators with varying leg lengths or mobility challenges. These extensions are typically made of barstock and can be clamped to the pedal2. Does your project include pedal extensions? Does this impact cover design or production costs?
-
Functionality and Durability:
- Wear Resistance and weather conditions: no need to mention, rubber pedals should withstand wear and tear due to frequent use. This means that all the rubber used should be durable and resistant to abrasion. Also, agricultural tractors operate in various weather conditions, so the rubber should be resistant to several atmospheric agents, including UV exposure, extreme temperatures, and moisture. This can have a tremendous impact on your choice for the best compound.
- Responsive: The rubber should, nonetheless, allow for precise control without excessive force.
-
Vibration Damping:
- Tractor pedals experience vibrations due to two main factors: engine operation and terrain. The rubber material should, therefore, dampen both to reduce the operator fatigue and improve comfort and health condition, especially if the operator has to endure long sessions onboard.
- Upper mold plate for the production of pedal rubber covers meant for agricultural tractors
- Another example of steel plate with ejectors for easier extraction.
- Testing of the same plate with extractors pushed up.
KIND OF RUBBERS COMMONLY USED FOR TRACTOR PEDALS:
So what about the rubber to be used? Alas, there is no simple, one-size-fits-all answer, as the compound used for tractor pedals can vary depending on the specific case. However, there some materials are more common than others. To make a long story short, EPDM could be a winning choice in many cases for a number of reasons (see below), but is not that simple and it may not apply to your specific case. So, here is a list of the most common rubber compounds that can be used for tractor pedals and further details on their main advantages or disadvantages:
-
Natural Rubber (NR):
Natural rubber derives from the treatment of latex obtained from rubber trees. Among its main advantages:
-
- It offers good elasticity, and flexibility.
- NR is commonly used for pedal covers due to its excellent grip properties.
- Downside: in case of extreme weather conditions or prolonged use, it may not be as durable as synthetic rubbers.
-
Styrene-Butadiene Rubber (SBR):
- SBR is a synthetic rubber combining, as its name suggests, styrene and butadiene.
- It provides good abrasion resistance and durability.
- SBR is cost-effective and, given its overall satisfactory performance, it is often employ to get a fair value for money on the whole project.
-
Ethylene Propylene Diene Monomer (EPDM):
- EPDM is a synthetic rubber known for its excellent weather resistance.
- It withstands exposure to UV radiation, extreme temperatures, and moisture.
- It ensures good adhesions to surfaces.
- Its resilience makes it a good vibration dampening material.
- EPDM is commonly used in outdoor applications, which makes it an excellent choice for tractor pedals.
-
Nitrile Rubber (NBR):
- NBR is resistant to oil, fuel, and other chemicals.
- It provides good adhesion and durability.
- NBR can reveal a suitable choice for pedals of those industrial vehicles that may come into contact with chemicals such as oils or other hydraulic fluids.
-
Neoprene Rubber (CR):
Not just crops: many tractors must widthstand extremely low temperatures, as is the case with this dozer used for snow plowing.
- Neoprene is a synthetic rubber with good resistance to weather, ozone, and oil.
- CR reveals effective when it comes to adhering to metal surfaces.
- It maintains flexibility over a wide temperature range.
- Neoprene is used in various industrial applications, including pedal covers.
-
Other Blends and Compounds:
- Sometimes, manufacturers choose to resort to custom blends or compounds based on specific requirements.
- These blends can combine properties from different rubber types to optimize grip, durability, and comfort according to the specific needs of the manufacturing company.
CONCLUSIONS
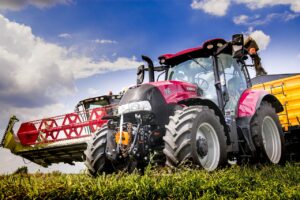
Agricultural tractor equipped with harvester. THe mechanical stress exerted by machine oscillations and ground conditions impose strict quality standard for the production of pedal rubber covers.
To choose the best compound for your tractor’s pedals, it is necessary to have a thorough understanding of the mechanics of the pedal in question, their purpose, use, structural and mechanical characteristics. So, in the end, the final decision is up to you, because the type of rubber used can vary depending on multiple factors. Of course, some materials, like EPDM, are used more commonly than others, but that doesn’t mean this applies to your case as well.
Hopefully, now you have a general overview that gives you a comprehensive view and allows you to make the right choice based on your field experiences and the specifications of your next project. And if you need further advice or consultation on mold production, don’t hesitate to contact us!